Firmametal’s hi-tech casting propriety processes consist of refining technologies and precision alloying techniques developed though extensive accumulated know-how, studies of melting techniques and associated R&D. As the demand for high-strength steel increases, so does the need for hi-tech casting. The production of these products, whose elongation and impact values are maintained at very high levels while their tensile-rupture resistance is also increased, requires extremely precise metallurgical processing techniques. Such processes are now available through a combination of steel refining and precise element selection and alloying route. Due to steel’s very high mechanical qualities, this product can only be produced in a special, customized manufacturing process when it falls out of the norm/demand values. The “hi-tech casting” means entire custom manufacturing propriety processes.
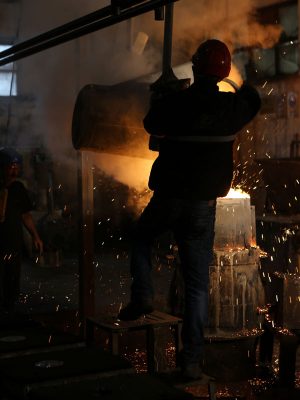
Steel and Siphero Casting
Utilizing advanced technology, Firmametal can supply sand casting variants of both Steel and Sphero casting; the most frequently used casting techniques.
Some specific special casting pieces are suitable for production as single castings or as small-scale serial castings. To achieve this, the metal is first melted is a special manner developed, in part, via Firmametal’s specialized skill-base and its accumulated experience. Following this, the molten steel is cast in specially prepared sand molds. Managing the steel’s solidification through the use of different mold sands while, also, managing the metal-mold reaction processes, together requires a major technical infrastructure.
In preparing the molten metal, the properties of the mold, the method of using the mold, the casting temperature and the structure of the mold sand are each of great importance due to the sensitivity of the process performed. Despite methodical work, any application defect can cause the product to fail to deliver the required properties. The targeted results cannot be achieved if the ranges of alloying elements and the alloying route included in the materials are not produced via the proper manufacturing methods. Firmametal can produce the important components required to deliver the expected quality levels and features. The company achieves this by undertaking both mass and custom manufacturing in partnership with other companies in its groups, and through its wealth of experience and know-how.
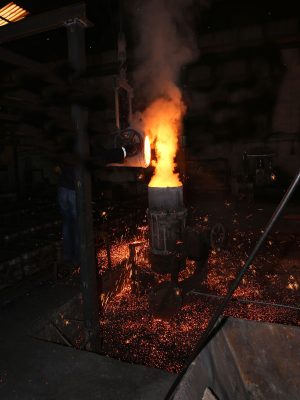
Die Casting
Used in the processing of nonferrous materials such as aluminum and zamak, die-casting is also used to produce precision components. Iron molds are used as the material to be processed are light and easily shaped. The sectors that demand light, high-strength components, such as the automotive and aircraft industries, utilize such products.
There are two types of die casting: “Pressing” and “Injection”. Pressing, utilizing cold-chamber machines, is suitable for metals and alloys with a melting point above 1000 °C. All melting processes are undertaken outside of the machine. The injection method, on the other hand, has the melting performed in hot-chamber machines. Here, two half-machines push the melted metal into the mold utilizing compressed air or a piston.
Ductile material is required for cold forging but it does produce stronger products. Intermediate-sized and small components are cold forged. Cold forging ends up with smoother surfaces that weave the component’s dimensional accuracy, better than hot forging. Having extremely high strength, cold forging is used particularly for fittings such as bolts and nuts.
Precision Production Techniques
Firmametal uses hi-tech casting techniques in both those operations that require advanced technology as well as in all of its standard production. With its specialized refining technology and experience in the material sciences, Firmametal exceeds customers’ quality expectations. Hi-tech casting, sought after mainly by the heavy machine industry, requires the use of precision casting techniques. Firmametal has a proven experience with major products including bearing boxes for locomotives, steel plants heavy duty high strength parts and medium temperatures resistances pellet cars, battle tank armor and their high strength machinery parts, High tonnage press body frames and their parts, cavitation resistance hydraulic turbine runners for power generation plants and their parts, severe corrosion resistance vanes, pumps, casings and discs, high temperature creep-rapture resistance parts.