Forging is the hot, warm or cold process of component forming utilizing only an applied force. Forging is completely different from casting as forging strengthens textures by deforming the existing atoms’ spatial relationships. Forging satisfies the need for components that require high strength and toughness but are not molded, as in casting. Many components, including bolts, rivets, bars, turbine runners, gears and hand tools are produced by forging.
Hot Forging
Hot forging process require moderate strength and are more suitable for larger components. The internal grain patterns along with the complete structures of the components are softened by heating are then rounded and shaped using a forging press, following which they are left to cool. This type of forging, in which component sizes can not be so precise, is also not as effective as cold forging in terms of surface roughness because it leaves behind an oxide and needs for further processes. It is a type of manufacturing used in by components whose tensile-rupture-elongation and pulse resistances should be higher than those delivered by casting. Hot forging is used in the production of construction clamps.
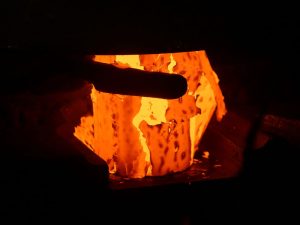
Cold Forging
Ductile material is required for cold forging but it does produce stronger products. Intermediate-sized and small components are cold forged. Cold forging ends up with smoother surfaces that weave the component’s dimensional accuracy, better than hot forging. Having extremely high strength, cold forging is used particularly for fittings such as bolts and nuts.
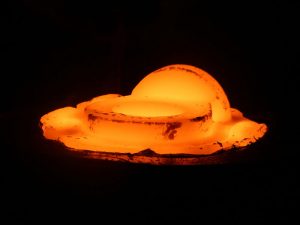
Forging Technology
Firmametal uses its materials sciences expertise and experience in the determination of mold tolerances, component tolerances and the structural tolerances of materials to be used. These are all significant to forging technologies. With forging experts from throughout the company group undertaking extensive R&D, Firmametal plays an active role in ensuring material quality during material procurement. For the design and processing of cold forging operations, Firmametal discusses with its forging experts the work to be done down to the last detail and establishes the necessary guidelines. All of the company group’s experts work together in determining which heat treatment is to be applied, the materials to be used and their structures, and from where to procure these materials. Firmametal brings the product to its designed form using the required intermediate heat treatment to overcome Hydrogen embrittlement, before utilizing the company’s materials science expertise and experience in the galvanization stage. The product, now kiln-dried, becomes either a colored or uncolored product